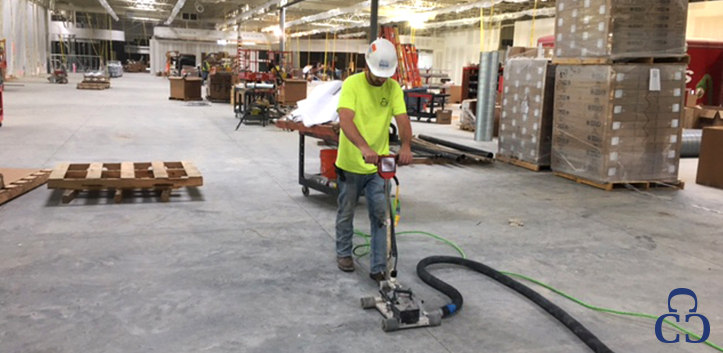
Polished concrete may seem fairly straightforward.
Take a concrete slab and make it shiny, right? In short, this holds true. But there are two distinct and different ways of getting to this point.
Some contractors may be less than transparent about these processes. The end product may only seem identical on the surface, leading to problems with polished concrete floors in the end. We’re going to dive a little deeper to show you what’s really going on.
Mechanical Polishing
We’ll start with the mechanical process – it requires a little more effort and time to complete.
There are many stages of grinding and polishing the concrete slab that each prepare the surface for the next. Grinding too much too quickly with a planetary floor grinder can leave an uneven surface, making further polishing extremely difficult.
Care is taken to ensure that the concrete is evenly filed down with diamond abrasives. At first, large, deep scratches are left in the surface. As polishing grit size is reduced, these scratches become smaller and smaller until they don’t appear visible to the naked eye.
When scratches are this tiny, the “peaks” and edges of the scratches aren’t susceptible to breakage. This filing remaining intact is key to the floor’s ability to resist wear and tear.
The mechanical method is not completely free of chemical help. A densifying chemical is used to fill the pores in the concrete’s surface. This isn’t an artificial enhancement to the polishing process; it only makes mechanical grinding easier and more effective.
Topical Polishing
Surface polishing with the help of an additive is the cheaper, less time-consuming method of concrete polishing.
The process starts similarly to the mechanical method. Grinding abrasives on a planetary floor grinder are used to prep the surface. However, the key difference is that grinding stops much earlier and at a much more coarse grit level.
At this stage, a chemical sealer is applied. It fills in the considerably large scratches and gaps in the surface of the concrete, creating a glossy finish. Initially, this creates a decent finished product.
The problem, however, comes from wear. The large “peaks” left in the ground concrete surface are prone to smoothing and/or breaking, meaning that the floor becomes worn even with the chemical polish. When surface breakage occurs, the gloss is compromised and allows dirt or moisture to seep in.
Abrasive Residue
Another thing that can cause the integrity of polished concrete to be low from the start is residue from a cheap abrasive.
Diamond polishing pads are attached to a planetary floor grinder and held together by resin. If this resin is particularly cheap or there’s much more resin than diamond particles, it can be transferred to the concrete’s surface during polishing.
This creates the illusion of a well-ground, smooth surface when it’s actually composed of only melted resin. This gloss of this resin will wear even more quickly than chemical sealant, creating problems with polished concrete floors in the long run.
Put simply, it pays to make sure your grinding abrasives are of high quality.
Identifying a Good Polishing Job
Although topically-polished concrete may appear very similar to a mechanically-polished floor, there are ways to tell the two finishes apart.
Lights will reflect very clearly in a mechanically-polished surface because the concrete itself is actually flat. A topical chemical sealant is only the top layer on uneven concrete, meaning that light is distorted in its reflection. Topically-polished surfaces show unclear areas of light with “tails” going out in any given direction.
Hopefully, these tips have helped inform you enough to properly judge the polishing job of any contractor.
******
Custom Concrete Creations is chosen to help facilitate projects because we are the preferred custom concrete floor company, not only in Omaha, but for the greater Midwest region. No project is too big or too small for our team of seasoned experts who use state-of-the-art equipment on each and every project. We help you achieve the look of your dreams and do not consider the job done until you are happy with the results. So give us a call or contact us for your custom concrete needs today!