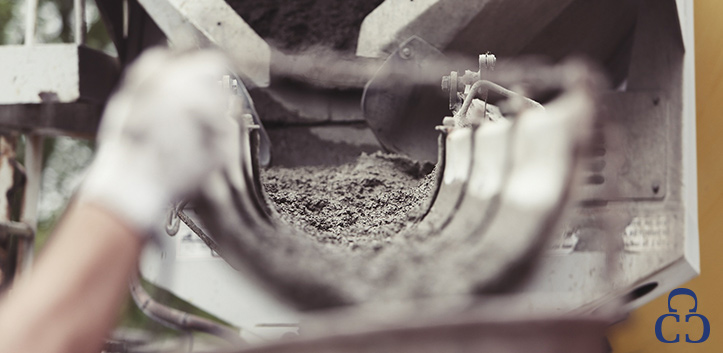
Cement is one ingredient – if not the key ingredient – in the industrial concrete that builds much of the world around us.
Cement is combined with water to form a paste. This is used to bind together crushed stone, sand, or gravel. Concrete is the compound formed by this mixture.
Seems fairly straightforward, doesn’t it?
In a way, it is. But the cement production process actually contributes to sizeable CO2 emissions.
Portland cement is the most common variety. In 2017, the energy costs related to its production added up to more than $7 billion globally.
The Production Process
Some of the main components that begin the production process include clay, iron ore, limestone, and shale. These raw materials go through multiple grinding stages (the beginning of considerable energy consumption) to reach a manageable size.
In order to fuse a super-strong compound, these ingredients are heated in a giant kiln.
The kiln itself is massive: 10 or 15 feet wide and sometimes over 300 feet long. To reach a temperature of 2,700 degrees Fahrenheit, waste or fuel is burned below.
The exact material that is burned depends on the plant. Tires, wood, plastics, gas mixtures, or coal can be heated in huge quantities to prepare the cement. This heating process, called pyroprocessing, is responsible for nearly three-fourths of overall energy consumption for cement.
In addition, CO2 is naturally emitted during limestone calcination. The extreme heat separates the inherent carbon dioxide from the raw materials and forms new silicate compounds – a large part of what makes concrete strong and durable.
These natural emissions account for another four percent of total cement emissions.
When the fused raw material exits the kiln, it’s called “clinker.” Pellets of compound about the size of a marble are the prime ingredient in industrial concrete. First, though, they must be ground into an ultra-fine dust. The electricity used to accomplish this makes up the rest of cement’s total energy footprint.
How Can We Change It?
A Kentucky engineering school has been awarded a million-dollar grant to help fix the cement production problem.
The J.B. Speed School of Engineering are embarking on an ambitious two-year mission to help change the way industrial concrete is manufactured. The initiative is led financially by the Clean Energy Smart Manufacturing Innovation Institute (CESMII), who has also contributed tens of millions of dollars to other industries’ energy efficiency efforts.
Their goal is to reduce the five percent of global CO2 emissions for which cement production is responsible.
The grant research will focus on pyroprocessing and the massive fires that fuel it, according to project leader W. Mark McGinley, PhD:
“Energy is a significant portion of the cost of cement production. Controlling firing temperatures and times will reduce cost and environmental impacts. These improvements make this industry more viable through adoption of smart manufacturing technologies and processes, improve their product, and help the planet.”
They’re lofty claims, but industry data shows that they are viable.
Research has shown that cement kilns in the U.S. and Europe operate at an average of less than 35 percent efficiency, so there’s definitely room for improvement.
Emission-monitoring systems and temperature control systems could be keys to the solutions the industry needs. Another potential improvement involves the use of alternative firing fuels that would eventually become industry standards. Pre-treating these fuels with certain chemical agents has also been suggested to improve temperature precision.
Cement is crucial to industrial concrete. Hopefully, this research can follow through on its promise to turn the cement industry green.
******
Custom Concrete Creations is chosen to help facilitate projects because we are the preferred custom concrete floor company, not only in Omaha, but for the greater Midwest region. No project is too big or too small for our team of seasoned experts who use state-of-the-art equipment on each and every project. We help you achieve the look of your dreams and do not consider the job done until you are happy with the results. So give us a call or contact us for your custom concrete needs today!