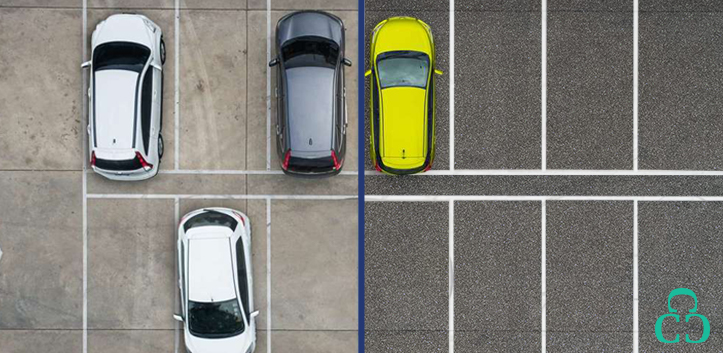
Parking lots: they’re quite literally everywhere. No matter their size or location, they all serve exactly the same purpose.
They’re some of the most straightforward custom concrete systems. Pour it, let it cure and finish it off with some painted lines.
Yet, there’s another option. Asphalt is an equally popular surface material. So, which is best?
It depends on a number of factors including the installation process, environment/climate, short- and long-term maintenance, lifespan and, of course, cost.
We’ll touch on these important topics to compare the pros and cons of each type of parking lot project.
The Initial Installation
To cut right to the chase, asphalt is the quicker installation if time is your only concern. Liquid asphalt is used to bind together the bits of rock and gravel instead of cement, as is the case with concrete.
There’s one emerging problem, though: asphalt is getting pricey. The Federal Bureau of Labor Statistics found that the price of asphalt increased by 250 percent in just five years. This is due to the fluctuation in crude oil prices, since liquid asphalt is produced during the oil refinement process.
As with any construction project, the surrounding environment dictates the methods of construction. An asphalt parking lot can be ready for use in as little as two days in some climates.
The cost of a concrete parking lot pour tends to be higher compared to asphalt , which we’ll explain further below.
Maintenance Cycles
After the curing period is complete, both materials should be sealed. Asphalt needs up to six months to fully cure for sealing, while concrete only has to sit for a few weeks. Ideally, joint fillers and sealants must be applied every two or three years for either type of surface.
The reapplication of liquid asphalt every few years can become costly. The lower pavement layers are more permanent, but the surface requires new coats and total resurfacing every decade or so. This asphalt maintenance can add up to almost 80% of the cost of initial installation.
Most custom concrete systems only requires joint work and simple cleaning. It is more rigid and strong than asphalt, but this makes it more brittle and gives it a higher risk of cracking under certain conditions.
The Climate Matters
In general, asphalt is more reactive to hot weather. Most people who live in areas where it reaches 100 degrees in the summer can easily conjure up the smell of sweltering asphalt on a hot day. Its black color automatically makes it more susceptible to the sun.
In extreme cases, an asphalt lot can also become slippery in heat due to its oil content.
Concrete changes more in cold weather than hot, and is more stable in warmer climates than asphalt. In the winter, though, concrete contracts and expands with freeze/thaw cycles more than asphalt. The latter, however, doesn’t deteriorate from the application of salt melt.
Total Cost of Ownership
The most important part of the concrete versus asphalt paving debate is the total cost of ownership (TCO), including maintenance.
A Minnesota Department of Transportation pavement study found the average concrete surface needs reapplication of joint fillers and sealants every 28 years, while an asphalt surface requires repair every 16 years.
The same study found concrete to last anywhere from 30 to 40 years, whereas asphalt lasts between 15 to 18 years.
In total, concrete can cost nearly 30 percent less than asphalt over the course of its working life.
******
Custom Concrete Creations is chosen to help facilitate projects because we are the preferred custom concrete floor company, not only in Omaha, but for the greater Midwest region. No project is too big or too small for our team of seasoned experts who use state-of-the-art equipment on each and every project. We help you achieve the look of your dreams and do not consider the job done until you are happy with the results. Give us a call or contact us for your custom concrete needs today!